Enhancing Safety Measures During Equipment Maintenance And Repair
5 Mins Read
Published on: 17 June 2023
Last Updated on: 08 January 2025
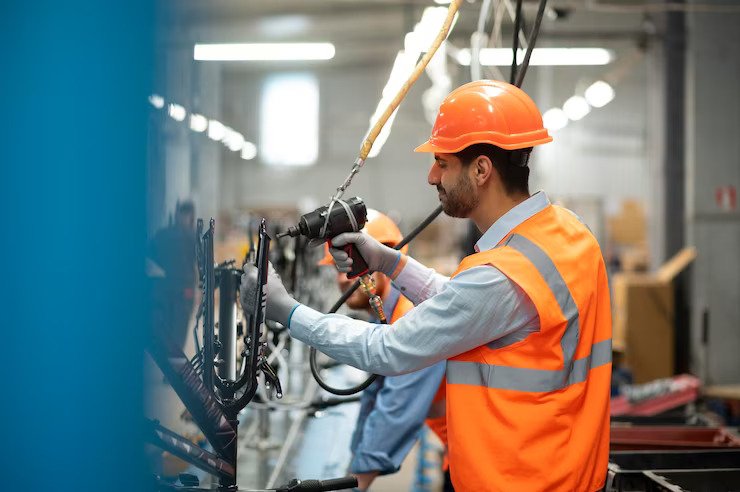
toc impalement
As technological advancements continue to pervade all aspects of our lives, the presence and importance of equipment maintenance and repair are undeniable. However, the act of maintenance and repair of these complex machines can be a dangerous task.
Thus, it is essential to identify and mitigate potential risks during these processes. In this article, we delve into safety measures to be enforced during equipment maintenance and repair to minimize accidents and enhance overall safety.
Understand the Equipment and Associated Risks
Firstly, understanding the specific equipment and its associated risks is a crucial step toward ensuring safety. This involves studying the machine’s manual and being informed about potential safety hazards. It is also necessary to understand the safety features of the equipment to use them effectively during maintenance and repairs.
In addition, performing a risk assessment is vital. It should include identifying potential risks, analyzing these risks, and taking measures to control them. Such proactive measures can prevent accidents and ensure the safe execution of maintenance and repair tasks.
Safety Training
One of the most efficient ways to prevent accidents is through safety training. Training can equip technicians with the skills and knowledge they need to handle various equipment safely. It can also help them identify risks and take the necessary precautions. Safety training should include both theoretical knowledge and practical demonstrations, to help trainees get a comprehensive understanding.
Moreover, safety training should not be a one-time event. Regular refresher courses can help workers stay updated with safety protocols, technological updates, and changes in work processes.
Personal Protective Equipment (PPE)
Wearing the appropriate Personal Protective Equipment (PPE) can provide a significant layer of protection during equipment maintenance and repair. PPE can include items such as gloves, hard hats, safety shoes and even more sophisticated items like safety glasses with distance correction. These items can protect workers from specific hazards associated with the equipment they handle.
Ensure that all workers are trained on how to use PPE correctly. Also, check that PPE is in good condition before use. Damaged or faulty PPE can provide a false sense of security and lead to accidents.
Lockout/Tagout Procedures
Lockout/Tagout procedures are essential during the maintenance and repair of equipment. These procedures involve isolating and securing energy sources to prevent accidental startup of the equipment during maintenance or repair. Following these procedures can prevent severe injuries and even fatalities caused by unexpected energization or startup of machines.
Make sure that all workers are trained on Lockout/Tagout procedures and that these procedures are followed consistently and correctly.
Regular Equipment Inspections
Regular equipment inspections can help identify potential issues before they become significant safety hazards. Inspections should be thorough, covering all aspects of the equipment. It should include checking for wear and tear, proper functioning of safety features, and potential faults in the equipment.
Document the results of these inspections for future reference. If any faults are discovered during the inspection, ensure they are repaired promptly to prevent accidents.
Safe Work Practices
Establishing safe work practices is another critical step toward enhancing safety during equipment maintenance and repair. These practices can include having a clean and organized workspace, using tools correctly, and following established procedures. Safe work practices also involve knowing when to stop work if a situation becomes unsafe.
Encourage workers to communicate openly about safety concerns. A culture of safety can go a long way in preventing accidents and enhancing the overall safety of workers.
Emergency Response Plan
Despite all safety measures, accidents can still happen. Therefore, it is crucial to have an emergency response plan in place. The plan should outline the steps to take in case of an emergency, including who to contact, first aid procedures, and how to evacuate the area if necessary.
Train workers on the emergency response plan and conduct regular drills to ensure that everyone knows what to do in case of an emergency.
Smart Devices for Industrial Applications
The integration of smart devices in industrial applications, particularly in equipment maintenance and repair, has transformed the way safety measures are enforced.
These devices, including condition monitoring sensors, are increasingly being used to observe conditions, forecast potential issues, and even automate certain maintenance and repair tasks. By doing so, they reduce the need for human intervention, thereby lowering the associated risks.
Condition Monitoring Devices (CMDs)
At the heart of most CMDs are condition monitoring sensors. These are a type of smart device specifically engineered to track the health and performance of machinery. They continually gather, process, and interpret data from equipment, enabling predictive maintenance and significantly reducing unexpected downtime.
Condition monitoring sensors are adept at providing real-time updates on various parameters of a machine, such as vibration, temperature, and humidity levels. This continuous monitoring can help pinpoint anomalies and trends that indicate a potential fault or failure before it occurs, permitting timely intervention.
Enhancing Safety Measures with CMDs
By forecasting equipment failures, CMDs equipped with condition monitoring sensors can significantly enhance safety measures. Firstly, they lower the chances of unexpected equipment breakdowns, which can pose serious risks to workers involved in maintenance and repair tasks. Secondly, they reduce the frequency of manual inspections needed, thus limiting human exposure to potentially hazardous environments.
It’s crucial to note that CMDs and their sensors should be integrated into an organization’s comprehensive safety approach. Workers need to be trained on how to interpret the data provided by these sensors and take appropriate actions. CMDs are not intended to replace traditional safety measures, such as PPE and Lockout/Tagout procedures, but rather to complement and enhance them.
Safer Maintenance and Repair Environment
Safety in equipment maintenance and repair is not an option but a necessity. It requires a comprehensive approach, including understanding the equipment, safety training, using PPE, following Lockout/Tagout procedures, regular equipment inspections, implementing safe work practices, and having an emergency response plan. By following these measures, we can significantly enhance safety during equipment maintenance and repair, minimizing accidents and creating a safer work environment.
Read Also:
Comments Are Closed For This Article