What is the Function of the Solenoid Valve?
4 Mins Read
Published on: 05 March 2022
Last Updated on: 14 November 2024
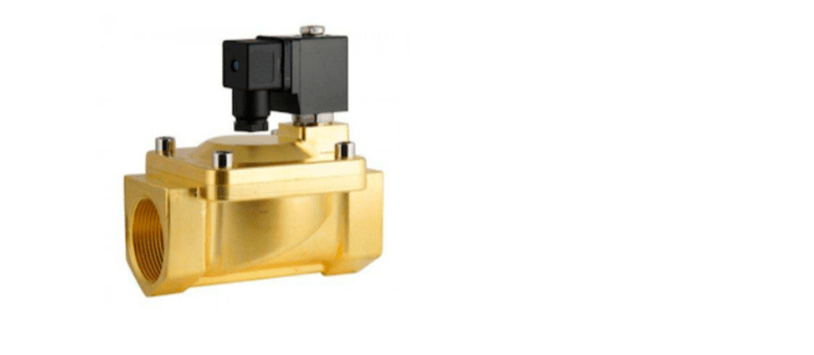
toc impalement
Solenoid valves are electromechanical devices used to control the flow of liquid and gases. They consist of two parts: a solenoid (electric coil) with a movable centrally-located plunger (ferromagnetic core) and a valve body. These valves find applications in various settings, and their use cases depend on their circuit function, the principle of operation, and the valve types. We’ve covered these and more below.
How Solenoid Valves Work
When a solenoid valve is in a rest position (assuming it’s normally closed), the small orifice is closed by the plunger, so there’s no fluid flow. When the electric current goes through the coil, it makes a magnetic field with a resultant magnetic force.
This force overcomes a spring force that holds the plunger in place. As the plunger is pulled upwards, the seal opens and allows the fluid to flow.
For the normally open solenoid valves, the plunger would be pushed down to close the orifice when current is passed through the coil. AC solenoid coils come with a shading ring that helps prevent humming and vibration. This enhances a smoother operation.
The detailed working principle of solenoid valves depends on their unique design. Based on the working principle, we have three categories of solenoid valves. These are:
Direct Acting –
With this type, the maximum operating pressure and the flow rate are directly proportional to the solenoid’s magnetic force and the orifice diameter. These valves require no pressure difference and are used for small flow rates.
Indirect Acting –
They use the pressure differential of the fluid media to open and close the orifice. A pressure differential of 0.5 bar is the minimum required for this valve to operate. It also comes with an extra pressure chamber that allows the valve to control a relatively large flow rate. However, they only enable fluid media to flow in one direction.
Semi-direct Acting –
This type combines the properties of both direct and indirect solenoid valves. That means they can handle fluid with zero bar and even those with a high flow rate. The design and structure of semi-direct acting valves resemble that of an indirect valve, except that they come with more powerful coils; hence they consume more power.
Solenoid Valve Circuit Functions
Solenoid valves are used to open, close, dose, mix or distribute gases or liquids. The specific use case of these valves will depend largely on its circuit function. There are two main circuit functions: a 2-way and a 3-way solenoid valve.
Figure 2: 2-way valve
2-way solenoid valves have an inlet and an outlet port. This valve is used to either close or open an orifice, and its flow direction is key to obtaining proper operation. On the other hand, 3-way solenoid valves have three ports. Since the valve has two states, it can switch between two circuits. 3-way solenoid valves are used to close, open, mix or distribute fluid media.
Figure 3: 3-way valve
Solenoid Valve Types
Solenoid valves can be broadly grouped into three types: normally closed (NC), normally open (NO), and bi-stable types. The NC types are always in a closed position unless an electric current passes through the coil. For the NO types, the orifice is always open, meaning the fluids will flow in the rest position and only stop once an electric current is applied to the coil.
On the other hand, bi-stable solenoid valves are neither NC nor NO. Instead, it’s a latching valve that can be switched on and off by a momentary or instantaneous power supply. Once a momentary current passes the coil, the valve changes its current position and stays in the new state until a transient current is applied again. This type uses permanent magnets instead of a spring.
Solenoid Valve Selection
Before choosing a solenoid valve, it’s necessary to understand the working principle, circuit function, type (whether NO or NC), and most importantly, your unique applications. Here are the other factors to consider:
i. Housing and seal material –
Ensure the valve’s housing material can withstand the temperature and the chemical properties of the fluid media is controlled. The internal components such as the plunger, seal, and spring should also be made of compatible materials.
ii. Response time –
This is the time it takes for a valve to go from one position to another. Directing acting valves with relatively smaller sizes often react more quickly than indirect or semi-direct valves.
iii. Pressure and temperature –
Ensure that the valve can withstand the minimum and maximum pressure for your unique application. This also applies to the operating temperature of the fluid medium.
iv. Approvals and certification –
Always consider the compliance standards and industry regulations before choosing a solenoid valve. Safety standards, IP rating, and quality of the material and parts are key aspects that determine certification and approval of valves for specific use cases.
Endnote
Solenoid valves find applications in various industrial and domestic settings where fluid media must be controlled. Even so, these valves can only be used for clean gases and liquids. Common use cases include irrigation systems, refrigeration systems, air conditioning systems to control air pressure, car washes to control water and soap flow, etc.
When choosing a solenoid valve, always pay attention to your needs and the unique valve features. Similarly, check the manufacturer’s reputation, customer experience, warranty, etc., before making up your mind.
Read Also:
Comments Are Closed For This Article