Implementing Efficiency Improvements in Your Industrial Facility
06 May 2025
5 Mins Read
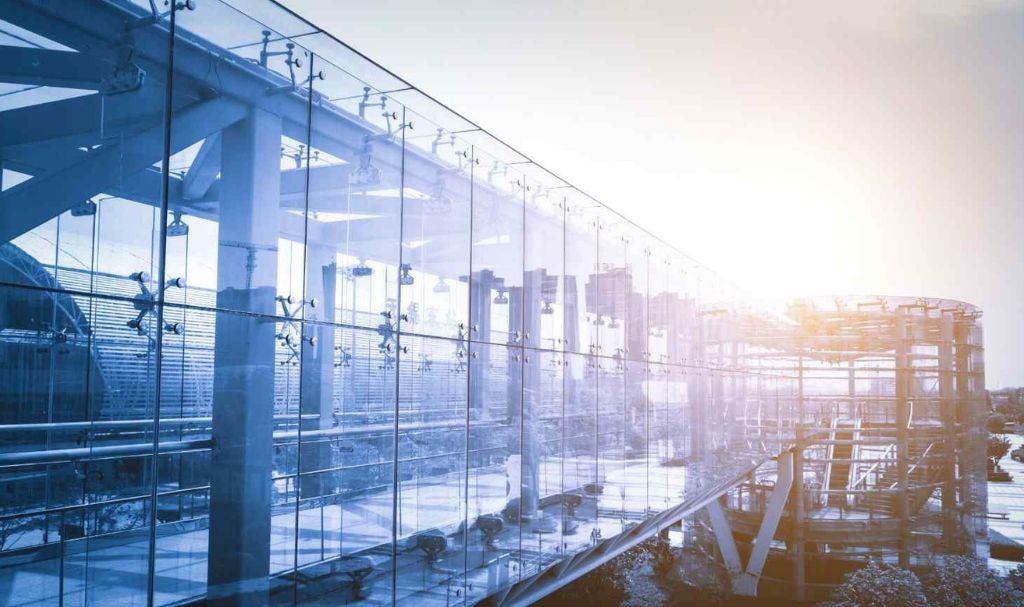
toc impalement
Key Takeaways
- Discover how minor adjustments can lead to substantial gains in industrial efficiency.
- Recognize the importance of regular evaluations and employee skill enhancement.
- Investigate how technology is transforming facility management for the better.
To stay competitive in the market and meet consumer demand, it is important to improve industrial efficiency. Although the main operations and business functions are different for various industries, industrial efficiency improvement can boost organizational performance.
Moreover, it can help you to adopt diverse sustainable measures and practices for your firm. This can give you a unique brand value in the market, helping you to attract different consumers.
Additionally, when you improve your industrial efficiency, you get maximum output for minimum inputs. That is, it reduces your resource consumption, operational costs, and enhances production and manufacturing.
But, how to improve this industrial efficiency for your business? Worry not. We have brought you a complete guide on how to improve industrial efficiency.
Keep reading to know more!
Steps to Take for Industrial Efficiency Improvement in Your Facility
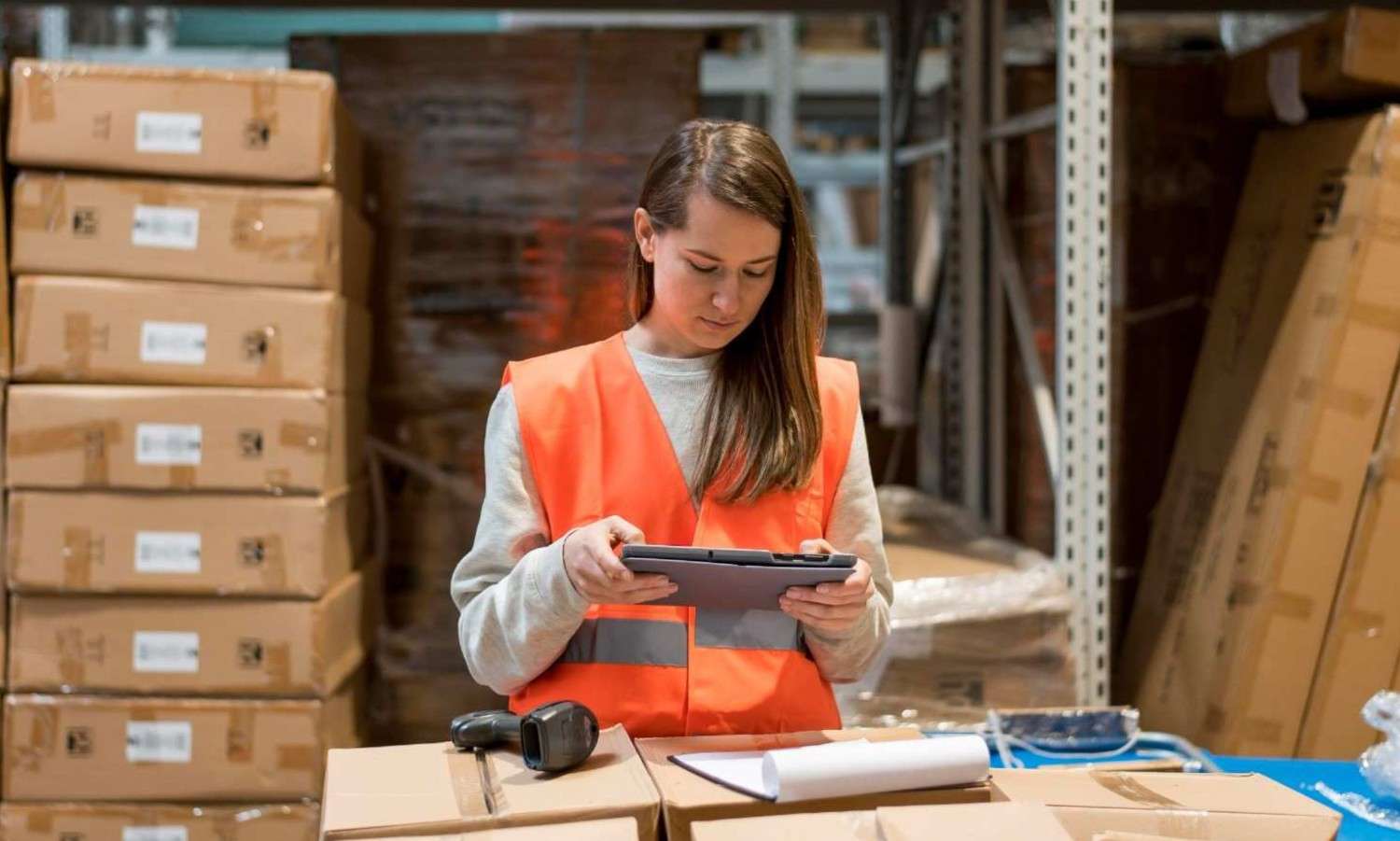
In order to enhance your organizational performance and utilize sustainable industry practices, you should focus on improving your facility’s efficiency. By taking proper measures and following the steps, you can improve it easily.
Here is the step-by-step guide for industrial efficiency improvement of your facility.
Start with an Efficiency Audit
An efficiency audit is essential before making any improvements in an industrial facility. So, you should start this entire process with the efficiency audit for your facility.
When you conduct the efficiency audit, you will be able to identify the specific areas of energy waste, equipment inefficiencies, and operational bottlenecks.
Also, you can assess how much energy is consumed in power supply, operations, equipment maintenance, and workflows. And, based on this analysis, you can find strategies and ideas to increase productivity while reducing the operational costs.
Moreover, with an audit, you can ensure compliance with the industry standards and sustainability goals. This makes it a critical first step for maintaining long-term efficiency improvements.
Once inefficiencies are identified, you can work with major industrial suppliers in North Carolina to source high-quality equipment, energy-efficient components, and automation solutions.
Also, upgrading outdated machinery, optimizing supply chains, and implementing innovative technologies can help you to lower costs and improve performance.
Upgrade to Modern Equipment
Old and traditional equipment can hinder your overall operational performance. It will need constant repair costs and more energy consumption for limited production.
So, it is important to upgrade to modern equipment to improve your industrial efficiency. Investing in modern equipment for your facility can significantly lower the resource waste, maintenance costs, and energy consumption.
Moreover, the modern machinery and industrial equipment are designed with energy-efficient components. This helps in improving the performance and maintaining industrial safety measures.
Also, upgrading your machinery can help you to minimize your environmental impact with a reduced carbon footprint.
You can also choose reliable suppliers to acquire high-quality, durable equipment tailored to your specific operational needs. This can help in fostering continuous improvement in operational effectiveness.
Prioritize Employee Training
Industrial success depends on the human element, making ongoing employee training is essential for skill enhancement and industrial efficiency improvement.
With your training methods, you should try to inform your workers about the industrial trends, new technologies, and safety standards. Given the rapid pace of innovation, existing practices can quickly become outdated.
You need to understand that when you properly train your employees at work, they can solve critical problems, operate machines, and change processes. Moreover, this can help in improving the overall industrial efficiency through product quality enhancement and reduced time.
Embrace Automation for Repetitive Tasks
Automation represents a transformative shift in how industrial facilities operate. By automating routine and repetitive tasks, you can reduce dependencies on manual processes that are susceptible to errors.
Moreover, by embracing automation, you can reduce human resource consumption, and use your employees for critical work. And, they can focus on solving important issues within the organization with problem-solving and analytical skills.
As you already know, integrated automation systems have significantly improved productivity in various manufacturing sectors. So, by harnessing these automated solutions, you can scale your operations efficiently without proportionately increasing the workforce.
This future-ready approach makes automation indispensable in today’s competitive industrial landscape.
Utilize Energy Management Systems
Adopting an energy management system has become essential for industrial operations seeking to improve efficiency in light of escalating energy expenses and growing environmental concerns.
With the help of an efficient EMS, you can monitor your energy consumption, spot inefficient trends, and take corrective measures. Also, the energy management system can help you to lower your energy consumption and convert to sustainable practices.
Moreover, incorporating EMS into facility management can facilitate compliance with environmental regulations. It can also help in enhancing energy efficiency and minimizing carbon emissions.
This proactive approach curtails unnecessary expenses and supports your sustainability objectives, reflecting positively on its environmental stewardship.
Consider Facility Layout Improvements
The layout of a facility plays a crucial role in its operational efficiency. An optimized layout minimizes the travel distance for materials and personnel, which enhances the workflow efficiency.
You can try to regularly evaluate and reconfigure your facility layout to ensure that the processes need no extra distance coverage. Also, your layout should be efficient in aligning the design with the requirements of the production.
Moreover, this adaptability allows you to respond more efficiently to changes, maintaining operational efficiency even during fluctuating demands.
Additionally, improvements in layout enhance safety by providing clear pathways and reducing unnecessary physical interactions. This can help you to provide a safer and more streamlined operation.
Encourage a Culture of Continuous Improvement
The success of industrial facilities depends on fostering a culture of continuous improvement. That is, your employees should actively identify the inefficiencies and suggest ideas for improvements.
Moreover, this collaborative approach empowers everyone involved, utilizing their diverse perspectives and expertise to improve operations.
And an inclusive culture promotes employee engagement and satisfaction. This can help you to ensure that there are incremental improvements resulting in significant efficiency gains.
Organizations can quickly adapt to market changes and maintain a competitive edge by making continuous improvement a core value.
Comments Are Closed For This Article