The Benefits of Using Bottle Capping Machine for Your Business
5 Mins Read
Published on: 02 March 2022
Last Updated on: 13 September 2024
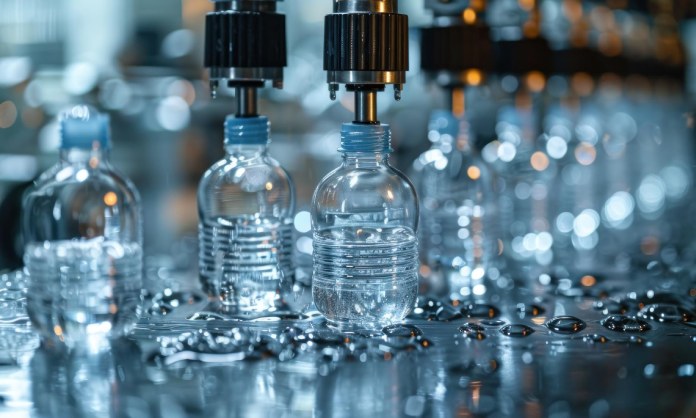
toc impalement
In the highly-digitized manufacturing and production industries, businesses are embracing automation at an arming rate. First-mover companies are already reaping the benefits of their investments, and other companies are following suit.
Capping machines are among the many tools used in nearly all industries to seal and tighten liquid or powdered products. Some of the common sectors where bottle capping machine are used include pharmaceuticals, agriculture, cosmetics, and food & beverages.
The type, design, and quality of capping machines used in each sector may vary. This is due to the different regulations and compliance standards that govern the production of specific products.
That said, capping machines are classified into three broad categories: manual, semi-automatic, and full-automatic capping machines. Under each category are further classifications, mainly based on their working principle, design, range of operation, speed, etc. These include inline cappers, rotary cappers, chuck cappers, spindle cappers, snap cappers, etc.
How To Choose The Right Capping Machine?
Before you choose a bottle-capping machine for your business, here are some of the benefits you may want to consider.
1. Speed and Efficiency
Fully-automatic and semi-automatic capping machines are generally faster than manual cappers. A fully-automatic inline bottle capper, for instance, can handle up to 350 caps per minute.
The increased production speed also means that more products are going to market with little human resources and within a short period. This translates to increased production efficiency, sales, and profits. Comparing the cost of acquiring a fully-automatic bottle capper to the cost savings in five or ten years makes it clear that automation has the upper hand.
2. Convenience
When you choose the right bottle capper for your business, you are eliminating redundancies and helping streamline the entire production process. A fully-automatic capping machine removes the need for human intervention. This means you can save space and minimize congestion on the production floor.
And by having the entire operations monitored from the control room by a few personnel, you also give your other employees time to focus on other important things, such as innovating new products and services.
3. Versatility
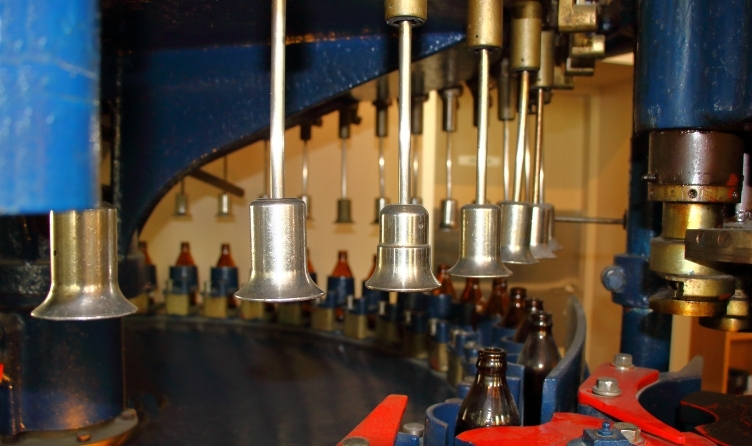
Machines, unlike humans, are more versatile and flexible. A fully-automatic bottle capper can handle different bottle sizes, materials, and cap designs. The chute ends can easily switch during operations to allow for this versatility without slowing down the production process.
Most modern bottle capping machine also use servo motors to enhance precise torque and speed control. This means you can easily adjust the operation speed and the load on the machine based on your production needs. Easy integration with the other machines in the packaging line is another advantage. That is, you can integrate a filling machine, a labeling machine, etc., without altering the efficiency or operational integrity of the cappers.
4. Consistency and Reliability
With bottle cappers, especially the fully-automatic types, you just need to feed in the production parameters, and the machine will handle all the heavy lifting. The benefit to this is that you are sure of consistent operations and reliable production, provided the machine is in good condition.
Similarly, machines don’t experience fatigue or take unexpected breaks like human labor. This gives businesses the option to estimate their production demands, from material sourcing sales to profits with high-end accuracy. Since the machines also stick to predetermined instructions, there’s less bias and no room for serious human errors. This translates to better product quality and reduced production risks.
5. Enhances Product Security and Integrity
In today’s highly dynamic and competitive market, product security and integrity are some of the key aspects that can either break or make your brand. Customers want to buy a high-quality product from a manufacturer with their best interest in mind. Bottle capping machines guarantees this through reliable seals and tightened closures that ensure the product is well secured.
Some cappers also come with tamper-evident packaging. This assures customers that the product they are buying isn’t only secure and original and from a specific manufacturer. Another feature that enhances product security and integrity is the clean-in-place technology common with capping machines that handle different bottle types and sizes.
The benefit of CIP technology is twofold. First, the machine does the cleaning; hence it’s fast and reliable. Secondly, no tools are required to open up the machine for cleaning. This reduces the chances of contamination from machine parts and elements such as grease, oils, dirty screws, etc.
Types Of Bottle Capping Machines
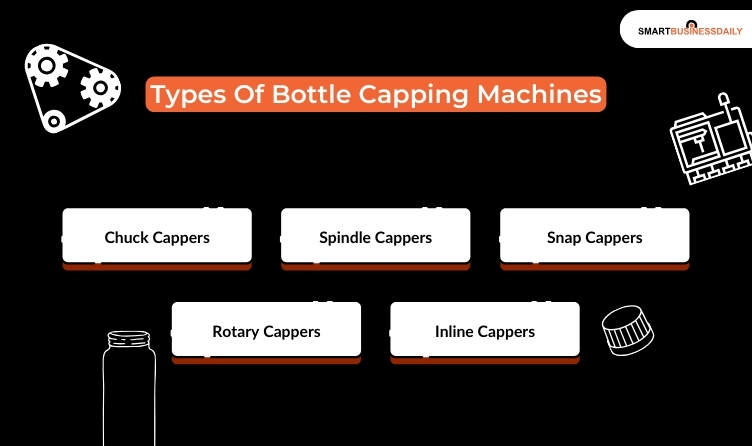
Bottle-capping machines come in all shapes and sizes. However, chances are that you might not need every kind for your business. Here are some of the different kinds of bottle capping machine(s) that you need to know about.
- Chuck Cappers: These capping machines use torque to screw or cap a battle. These machines usually cap glass soft drink bottles. The machine is highly precise and efficient.
- Spindle Cappers: These cappers use spinning disks to cap bottles. These machines are highly versatile and can be used to cap different kinds of bottles.
- Snap Cappers: These cappers use force to snap caps onto bottles. These machines are usually used to feed unthreaded caps. This form is one of the oldest variants.
- Rotary Cappers: These cappers come with multiple capping heads. These heads rotate and can cap large volumes of bottles at the same time. Therefore, these cappers are perfect for fast-paced production lines.
Inline Cappers: This variant of cappers is generally arranged in a linear format. The bottles move forward in a linear motion, and the whole process is done in one motion. This is the most convenient format of the bottle-capping machine. Therefore, they are the most popular as well.
Conclusion
Now that you know the benefits of a bottle capping machine, you want to invest in a reliable product that will serve your needs and last you long enough. When choosing a bottle capper, you always want to begin by assessing your production needs. That way, you can know whether a semi-automatic or fully-automatic capping machine is right for your business.
The other factors to consider are the available floor space, the nature of the products you are dealing with, industry rules and compliance specifications, etc. Similarly, you should pay attention to the manufacturer’s reputation, product quality and durability, warranty, and the availability of support and manufacturing services.
Additional Reading:
Comments Are Closed For This Article