4 Trends Making Factories and Manufacturing Plants More Efficient
4 Mins Read
Published on: 18 February 2022
Last Updated on: 09 September 2024
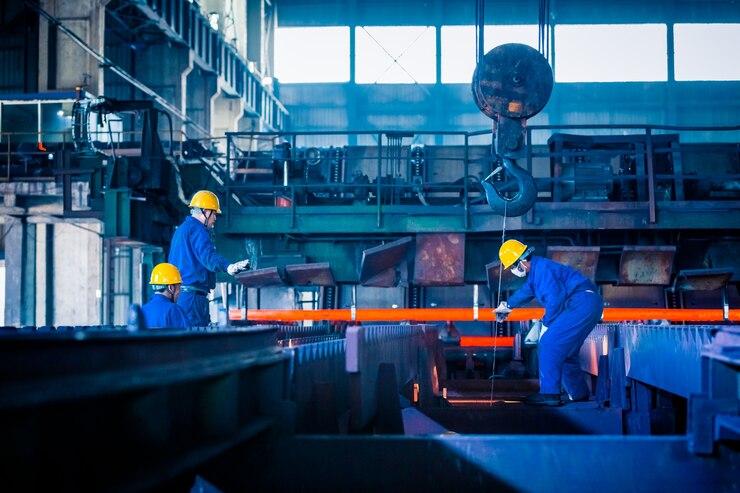
toc impalement
Manufacturing plants and factories are becoming more efficient each day. And it is all because of certain trends dominating the industry right now.
Today, we will be looking at some of the most popular trends that are helping to make these plants and factories more efficient.
Automating Mundane Tasks
Manufacturers often overlook the importance of certain tasks at their plants or factories. These can include packaging, applying labels, and much more. And while these tasks are mundane, speeding them up can make the supply chain more efficient.
However, increasing the speed alone will not do. Manufacturers also need to ensure efficiency. And thus comes the need for automating these processes or tasks.
Take automated industrial label printers as examples. An automated labeling printing machine can reduce the need for additional manpower to print and paste labels while delivering more accurate results.
These printing machines will save costs and make the overall supply chain faster as well as more efficient. Automated commercial label printers are the prime examples of how automating such mundane tasks can make things more efficient at manufacturing plants and factories.
An Oxford report suggests that automation technology can help the manufacturing industry generate $4.9 trillion more every year by 2030.
Another report claims that we can save almost 750 billion working hours if we can automate 64% of various manufacturing tasks. The possibilities are endless when it comes to implementing automation in the manufacturing industry.
Integrating the Internet of Things
The idea behind integrating the Internet of Things – IoT – in factories and manufacturing plants is very simple. IoT-based systems can sense, collect, and interpret data from the factory floors and then utilize that data to perform various actions. These systems became popular a decade ago but have started to gain more mainstream attention in recent times.
Embedding IoT in c helps make these places more efficient, as well as sustainable in ways. IoT technology reduces machine downtime. It also improves operational efficiency as it can reduce machinery breakdown.
That is possible because of early fault detection and mitigation practices, something we will discuss at a later point. And by reducing equipment failure, it becomes possible for these plants and factories to work as efficiently as possible.
IoT is also crucial at these plants and factories for monitoring the machinery in real-time. They are also used for generating accurate reports for better decision-making.
Thus, businesses that rely heavily on their production lines can make better business decisions and strategies through implementing IoT-based practices.
Ensuring Predictive Maintenance
Machine downtime in the manufacturing industry is a nightmare for businesses. Analyst firm Aberdeen Research surveyed this matter.
It shows that 82% of companies have had to deal with unplanned downtime over the last three years. And that cost each of them $260,000 an hour on average.
The cost of downtime for any of the Fortune 1,000 companies is even more expensive. These companies can lose as much as a million dollars an hour because of machine downtime. And in general, 98% of organizations report that it costs them over $100,000 for only a single hour of downtime.
Equipment or machine downtime is a curse to any manufacturing business. It not only hampers productivity and efficiency but also forces them to lose money. And the best way to deal with such machine downtime is by ensuring predictive maintenance.
Predictive maintenance is a form of early fault detection and mitigation practices in the manufacturing industry. Through predictive analytics, manufacturers monitor their equipment performance.
And by collecting and analyzing various performance metrics, they can get a good understanding of how the machines are performing. They can also predict when the machines might fail, and when will be the optimal time to send them for maintenance.
Predictive maintenance also requires manufacturers to perform various monitoring tests on their equipment. IoT plays a crucial role in such operations. Hence, it is an integral piece of technology in this trend.
Growing Popularity of Digital Twins
Simulations are vital in the manufacturing sector. Through simulating various aspects of their products, manufacturers can set definitive standards, and even verify different safety features. And more recently, they are working with such technology directly on their plant or factory floors.
Manufacturers use digital twin technology to visualize and simulate their entire supply chain. Using this technology, they can simulate their products and equipment, and see how the machines operate under different conditions.
Through digital twins, engineers can even predict breakdowns. The simulations will also help them set up maintenance plans.
Deloitte predicts that 70% of manufacturers in the US will start using digital twins in 2022. Many established companies are already making the most of it, like Boeing.
The airplane manufacturers have been using this piece of tech since 2018. They mostly use it to get a better understanding of how their airframes will perform over time.
As time passes, we will see more trends emerge. However, these trends will dominate the manufacturing sector for some time.
Read Also:
Comments Are Closed For This Article