How To Evaluate And Add New ERP Modules Without Disrupting Production
21 July 2025
5 Mins Read
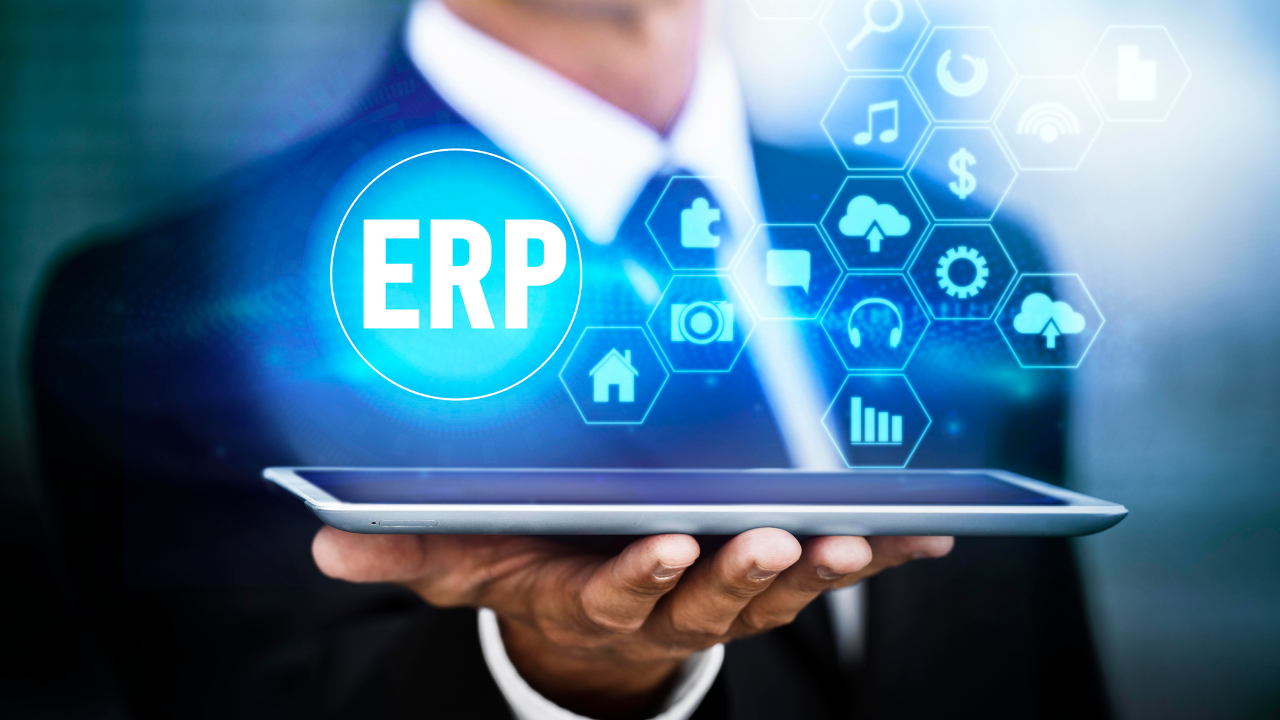
toc impalement
When manufacturing companies expand, they would always notice that their current ERP systems have become inefficient in supporting the changing running business processes. This can occur due to new product lines, market expansion, change in regulations, or customer requirements.
It is possible to fill these gaps by adding new modules to the existing ERP system, yet this process has to be done in a specific way, so that production will not be affected by it.
A new module may claim to offer improved scheduling, quality control, or advanced analytics, but failing to implement it properly will result in an expensive period of downtime.
Expansion should never be made without a clear concept of what is required during operations, quantifiable advantages, and the threat that shifting a system can carry.
Conducting A Thorough Needs Assessment
Before choosing any new ERP module, it is very important to review the current position of the system and identify where it lacks. The managers, shop floor supervisors, and IT personnel should be included in this assessment in order to get the full view of daily difficulties and process backups.
Their contributions make it possible to find out what functions really require improvements, instead of guessing or marketing by the vendors.
It should also be a process with the determination of future business targets in the next few years. As an example, a configure-to-order module may be necessary in case a manufacturer is going to offer more custom products. By matching the choice of modules to current issues of pain and future plans, the mutual relation of investments to business improvement is maintained.
Analyzing Compatibility And Integration
The introduction of new modules implies a lot more than switching on the additional functionality; one needs to integrate them into the current network of workplaces and processes.
Technical compatibility is an important consideration. Not all plug-and-play modules will not all the modules be and this particularly applies to modules of a core ERP that have been heavily customized in the past, or that are based on an older version.
Basic requirements of data and process alignment need to be scrutinized by the manufacturers as well. The new modules should conform to the same set of data definitions and interoperate with the records (existing records include bills of materials, routings, and production schedules).
Mapping of data flows has to be done cautiously to prevent repetition, inconsistency, as well as mistakes in live production.
Evaluating Vendor Support And Roadmap
When choosing a module, it should not be based on the existing features. By knowing the roadmap of the vendor, one hopes that the module will remain relevant as a change occurs in the industry.
Some questions, such as whether the module can support newer technologies such as integrating with IoT, mobile access, or complex analytics, should be asked. These can offer long-term value beyond the initial implementation.
The level of quality of vendor support and training is equally important. A module that gives the impression of being powerful and does not have good documentation or active support may well result in more time taken and overall cost.
The manufacturer ought to seek referrals from other corresponding firms that have installed the same module and gain from their experiences.
Planning A Phased Implementation
Any production environment is dangerous when applying a new ERP module at one go. A phased approach helps reduce that risk.
Beginning by pilot stage in one department or product line will help detect and resolve problems in order early. The pilot users feel free to give feedback that will streamline the processes prior to company-wide implementation.
Such a phased plan is to have details like timeline and milestones, and review points. Department heads and IT teams ought to define success on every step. This orderly launch of it can be used to keep the day-to-day things going and at the same time, advancing the project.
Prioritizing Training And Change Management
The most superior new user-friendly ERP module may not suffice unless the trainers teach them. Comprehensive training tailored to different user roles is essential.
As another example, the workers on the shop floor may require quick-reference cards, whereas supervisors may be redeployed through in-depth workshops that mainly concentrate on the report and exception handling.
Change management is equally important. Adding a new module can change responsibilities or workflows. Communication, including the explanation of the reasons why the changes are being done and how it helps the company and individual jobs, is clear, avoiding resistance.
Supporting users during the process of adjustment will contribute to a more quickly adopted product, with a reduction of errors.
Measuring Results And Continuous Improvement
The next important thing to do after go-live is gauging the performance of the new module. The measures may be less manual labor, accelerated reporting, or decreased scrap. By drawing comparisons with original objectives, it becomes possible to note whether the module is providing the desired value.
Continuous improvement should follow implementation. Feedback by the users will enable the detection of minor adjustments in workflow or reports that can facilitate their everyday use.
Periodic checks along the way, every so often, keep the module updated in line with the altering business needs and emerging changes in manufacturing ERP software.
Protecting Data Integrity And System Stability
The introduction of a module will involve transfer or duplication of data across the systems, and this comes at risks. Putting proper data verification practices in place will be one of the ways to identify problems before they impact production. This involves verification of consistency, completeness, and accuracy of data when running tests.
The easy way to protect system stability is to test run the new module in a test environment. This environment should closely mirror the live production system. It can be applied to teams in order to model real-life situations, check the performance, and make sure that implementation of the module does not hamper current operations and slacken workflow.
Building A Long-Term ERP Strategy
Lastly, a new module should be regarded as an extended ERP strategy but not a singular event. The manufacturers are supposed to constantly examine what aspects of the system are helping to run the operation and what may have to be updated or replaced within the next few years.
A long-term strategy allows focusing on future funding, elimination of the growth of technical debt, and maintenance of the whole ERP system that contributes to business growth and not a hindrance. That allows creating capabilities by manufacturers in an ongoing manner without jeopardizing the production process.
Read Also: