How To Scale Order Fulfillment Operations Without Losing Efficiency
21 July 2025
6 Mins Read
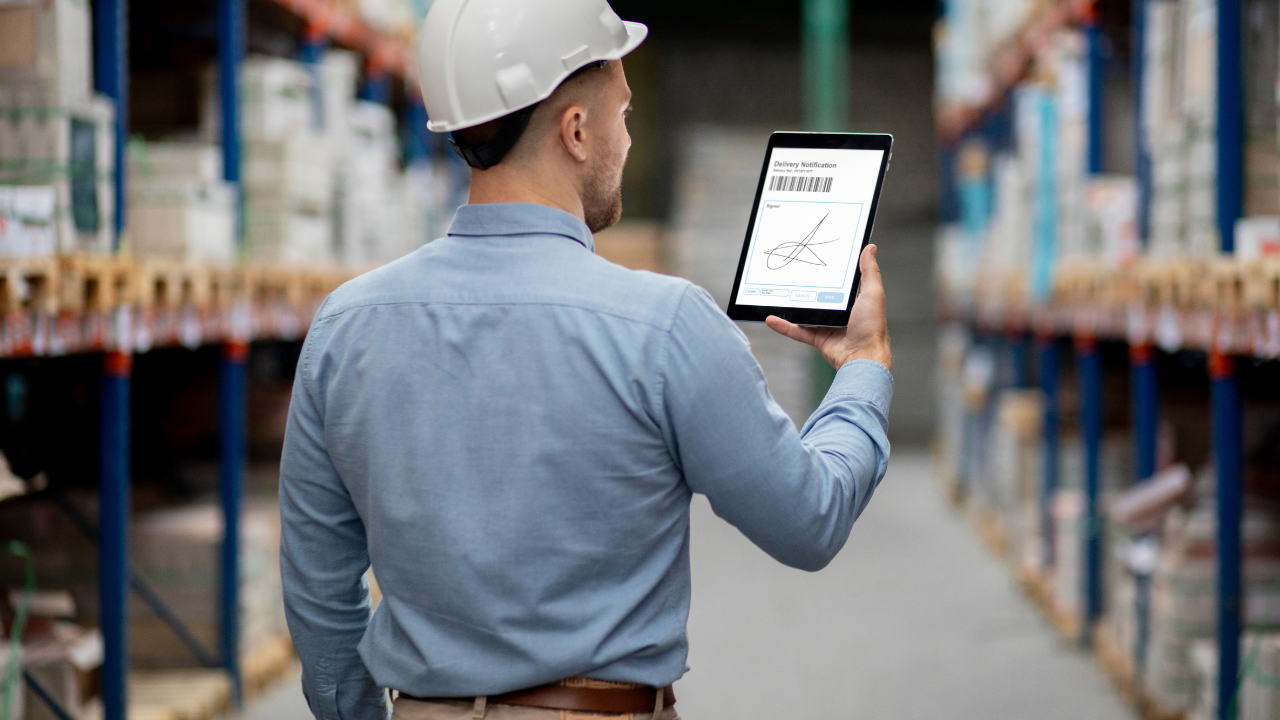
toc impalement
Remembering that most stores list a wide range of products, the more an ecommerce company expands, the more intricate the process of handling orders becomes. The issue is increasing capabilities to process more products and at the same time maintain speed, accuracy, and customer satisfaction.
Order fulfillment is a key business operation that ensures customer satisfaction and long-run business sustainability. Companies need to devise a way that does not raise cost, takes time, and provides quality as the scale is increased.
The expansion can be accompanied by introducing pressure on the current systems and processes of fulfillment. Yet, failing to plan and execute properly, the companies face delays, mistakes, and mostly spend more on them which ruins their reputation and profitability.
Businesses can address the demand without sacrificing their efficiency by scaling down their solutions, taking advantage of technology, and perhaps seeking the assistance of specialists. Such balance is of importance, particularly to those who use the ecommerce fulfillment services to accommodate their growing order volumes.
Assessing Current Fulfillment Capabilities
Scaling order fulfillment with the help of starting points on its way to development includes knowing the good and the bad about the existing operations.
Companies must perform an inventory of current warehouse area, employment rate, technology, and work processes. The evaluation assists in finding out the bottlenecks or inefficiencies that will only increase with order volumes.
Peak times and average order size are also pertinent to study in order to have a better picture of the future demand.
Given the knowledge of these operational aspects, companies will be able to identify whether their existing infrastructure can be optimized or there is a need to make new investments. A deep analysis develops a course on strategic scaling that does not contain any costly shocks and downtimes.
Implementing Technology To Improve Efficiency
Technology is critical in the process of scale fulfillment without loss of efficiency. Order management programs and warehouse management systems (WMS) have the capacity to automate most duties that are tedious with the increasing size of orders. These systems simplify inventory tracking, picking, packing, and shipping and minimize errors, and decrease speed.
The productivity is also increased by automation tools such as bar code scanners, voice picking, and conveyor systems that reduce the amount of manual labor. Incorporation of ecommerce systems and fulfillment systems allows data retrieval in real time, making accuracy high and communication with customers easier.
The location of the appropriate technology infrastructure allows the companies to cope with more rapid complexity without compromising the level of operations.
Optimizing Warehouse Layout And Processes
As order volume grows, efficient warehouse organization becomes essential. The rationalization of layout and storage techniques allows for lowering the travel time of pickers and handling shortcomings.
Organizing a product in easily accessible points which are of high demand and coming up with a rational picking route can increase throughput to a great extent.
Further, through standardized procedures and clear documentation, there will be consistency even with the introduction of new members of the staff during growth. Continuous training and performance monitoring help maintain quality standards.
Arguably, the primary determinant of how fulfillment can be scaled successfully without imposing excessive overheads and bottlenecks is a well-organized warehouse process.
Hiring And Training Staff Strategically
Staffing needs inevitably increase as fulfillment demands rise. However, adding more workers without the implication of training and management may result in a lack of efficiency.
Strategic hiring is the ability to predict the need to hire personnel in different orders in relation to the dynamics of orders and hiring temporary or part-time employees to meet times of peak performance.
The training programs must aim at developing process insight, accuracy, good safety, and the use of technology aids. Operation flexibility also arises when the employees are cross-trained to do various functions.
It is also essential to keep the employees actively invested and motivated enough to diminish turnover rates and preserve a high degree of productivity. A motivated and skilled workforce is an important resource in scaling up order fulfillment operations.
Partnering With Ecommerce Fulfillment Services
The cooperation on ecommerce fulfillment services is a feasible way out of the scaling issues to a great number of businesses. Utilization of a third-party provider of fulfillment enables the company to take advantage of infrastructure, technology and expertise that have already been established. This may make growth faster and keep costs down and the level of services.
The fulfillment partners usually offer scalable solutions capable of accommodating changes in order numbers, seasonal fluctuations, and geographical expansion.
Through working hand in hand with these providers, the companies are able to concentrate on the core businesses, i.e., marketing and product development, yet have confidence in the delivery of the orders.
The selection of the appropriate ecommerce fulfillment service is of high importance to the maintenance of efficiency at a time to deal with swift growth.
Enhancing Inventory Management
The proper organization of inventory contributes to scaling, as it eliminates inventory shortage and overages, which may interfere with fulfillment.
Companies must engage demand estimation technologies and information analytics to maximize the amount of stock and reorder frequencies. This minimizes holding costs while ensuring product availability.
Accuracy of the inventory is a necessity, because its inaccuracy may lead to delays and dissatisfaction of customers.
Frequent recounting of the cycles, real-time showing of inventory, and integrated systems are used to maintain correct inventory. Effective inventory management helps in the smooth running of the fulfillment activities and also offers an opportunity to respond quickly to changes in the market.
Improving Packaging And Shipping Processes
The last stage in fulfillment is packaging and shipping,g which influence customer satisfaction. Since more orders can be handled and thus the packaging process should be simplified to accommodate more throughput without compromising quality.
The pace can be accelerated through standardization of packaging materials as well as automation of the packaging stations.
The shipping strategies ought to be aimed at choosing the quality carriers on preferential terms, and the shipping software to be used to optimize the routes and monitor the shipment.
Being transparent and using proper tracking and delivery estimates earns the favor of customers. Packing and shipping of orders are essential to the maintenance of service quality without a scaling discharge.
Using Data To Drive Continuous Improvement
With the help of data collection and analysis, businesses can keep a clear eye on the fulfillment performance and find out where there is a need to improve.
The most important indicators of operational efficiency are the accuracy of orders, order fulfilment, shipping fees, and returns. Follow-ups on these indicators will reveal areas of inefficiency before they upset customers.
The process of continuous improvement is based on the formulation of clear objectives, the experimentation of a process change, as well as the implementation of employee and customer feedback.
The use of data-driven decision making ensures that the evolution of the fulfillment operations will be at pace with the business progress. This proactive approach safeguards efficiency and supports sustainable scaling.
Conclusion
To manage successful order fulfillment scaling operations, one should pay attention to an adequate combination of strategic planning, adoption of technology, management of workforce, and relationship management.
Through awareness of existing abilities to prepare in advance for possible problems, organizations can increase their levels of fulfillment without interfering with the quality of the services delivered. This growth is further helped by efficient inventory control, efficient packaging, and data-driven enhancements.
Indeed, ecommerce fulfilment services are a lifesaver to companies intent on growing rapidly and wish to retain operational quality. Finally, efficient scaling of fulfillment is an important determiner of business sustainability and customer experiences that lead to success in a competitive ecommerce environment.
Read Also: