Protect Those Parcels, With an Impact Detector
4 Mins Read
Published on: 28 June 2021
Last Updated on: 15 November 2024
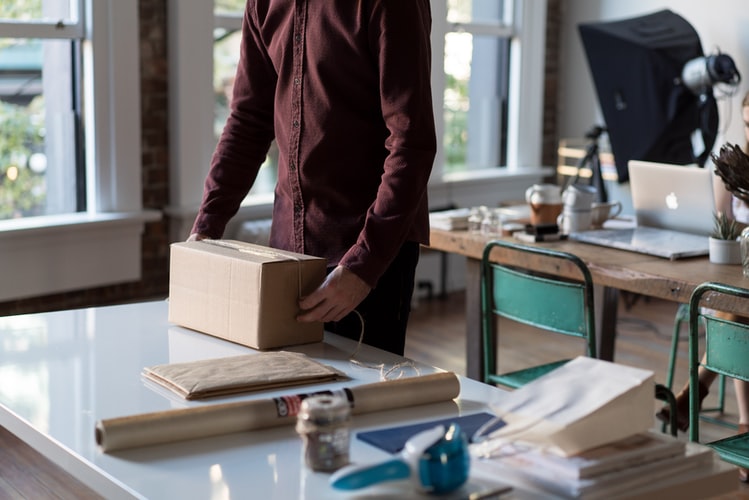
toc impalement
There are many ways parcels can be damaged before they reach their destination.
Consumers don’t like to get damaged products, though; receiving them can mean getting frustrated with the company they bought them from.
In some cases, that can also mean that they won’t buy from the company again because they don’t feel like they can trust it anymore.
That’s upsetting for the consumer, who might have liked the company or the product.
It’s also troubling for the company, as it affects the bottom line, and it may not understand why its products have many problems with its products.
Now, there’s a way to reduce those kinds of issues. It all starts with a tiny device that measures the impact the parcels sustain during shipping.
How Can Measuring Impact Change the Game?

Understanding a parcel’s impact during shipping is one of the best ways to ensure the items inside aren’t damaged. With an impact recorder, you can measure the strength of the impact on the parcels. The recorder will activate if the impact is outside a predetermined safe range.
That will let you see that there was an impact on the box or other parcel so you can take action to see if the contents have been damaged or destroyed by the impact.
The Advantages Of Using The Impact Detector?
The triggering of an impact recorder guarantees damage to the parcel’s contents. The objective is clear: to find the packages that have been mishandled to some degree.
However, a trigger does not mean that the package is damaged. Therefore, checking the content becomes seminal. This is why a trigger means a recall of the respective package.
Here are some advantages of using the impact detector.
- Impact detectors reduce the problem with shipping and handling.
- If that’s where the issue lies, it’s better to find that and ensure it can be addressed. Then, anyone concerned about the issue can focus on ways to adjust it.
- That, in turn, reduces the chances of having impact recorder problems for future shipments.
- This may help protect items in the parcels, but it can also help companies be more mindful of how they treat the packages they receive and those they ship out to others.
Rough Handling May Be A Surprise To Companies

It’s quite possible that the company shipping the parcels isn’t aware of how rough their employees are with the items that are being shipped.
However, impact detectors are an excellent way to show them they’re too careless with shipping from one point to another.
Determining where along the line the impact recorder is being triggered is important because that can help narrow down the point in the shipping process where problems are caused.
Changes at that point may significantly affect the shipping experience and the quality of the parcels being sent.
How The Detector Is Improving Customer Satisfaction

If a company doesn’t know that its employees are mishandling parcels and being too rough with them, that company can’t do anything to change that and make it better.
Here are a few ways the company can improve its customer satisfaction level.
- An impact recorder on each parcel is a great way to make employees more considerate and careful with their shipping parcels.
- With the help of impact, detector companies can track how well their employees are doing at shipping items safely, correctly, and without damage. While most companies and employees are careful, improvements can always be made.
- It is possible to set a predetermined level for an impact recorder; companies can easily see if their parcels are being handled too roughly.
- The more knowledge a company has about these things, the more it can make changes so that its supply chain and customer shipments operate more smoothly.
Types Of Commercial Impact Detectors
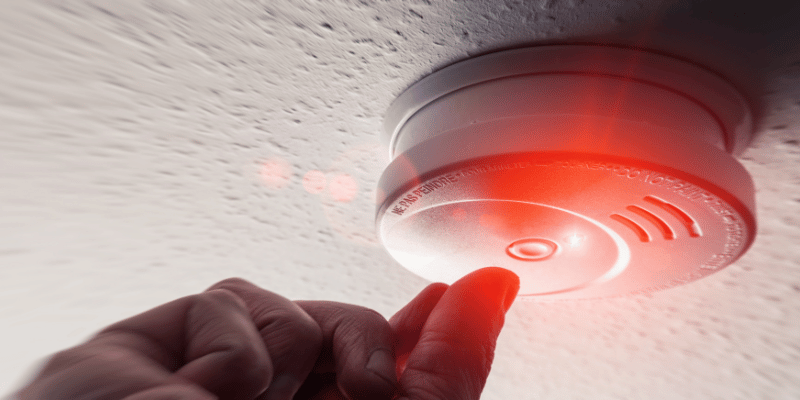
We have already discussed the importance of impact detectors extensively. However, we have yet to discuss the different kinds of impact detectors that are out there.
As of now, there are three different kinds of impact detectors. Each of them comes with its own set of pros and cons. Here is a brief overview of the commercial impacts that the delivery industry uses.
Shock Indicator Stickers
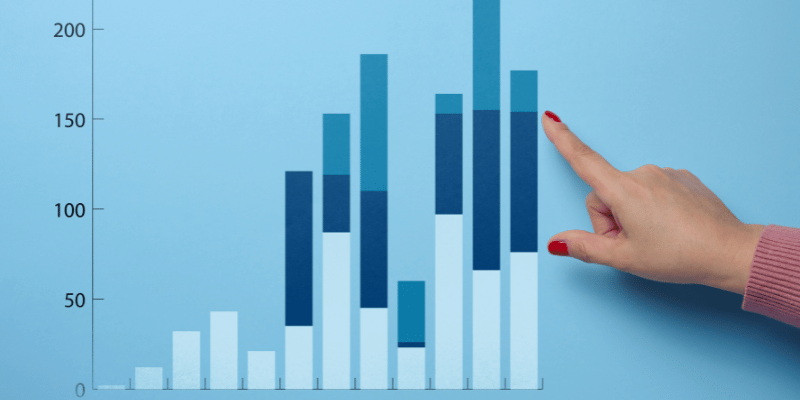
These are simple and effective in their execution. These stickers act like a visual marker that educates people about the nature of the product.
These sensors detect awkward angles and impacts. Therefore, your packages would be safe and sound.
Impact Sensors
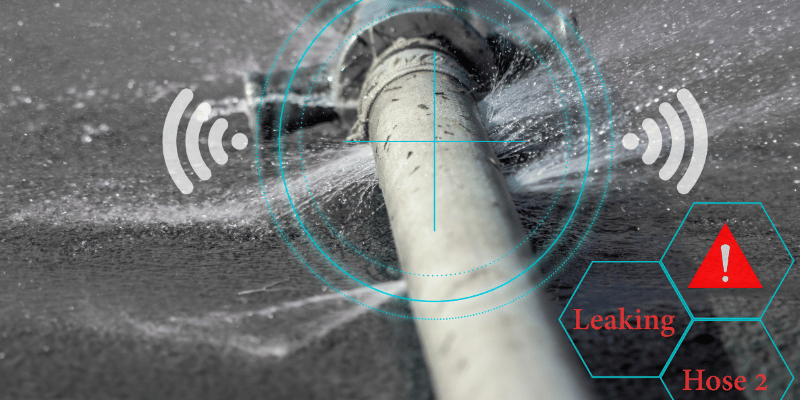
Impact sensors are also amazing and come in different shapes and sizes. As a result, impact sensors are perfect for managing and safeguarding packages from getting damaged.
These sensors are quite sensitive and can pick up the slightest of jerks. Hence, these are perfect for shi[[ing fragile products.
Shock Loggers
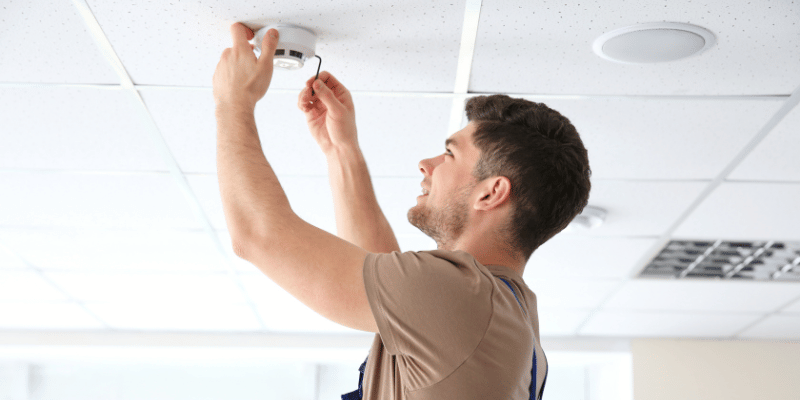
Shock loggers are the most advanced form of shipping protection system. These loggers record and monitor the whole journey.
This monitoring uses GPS data, impact data, and more to record and analyze the data. Therefore, they are comprehensive shipping protection equipment.
Conclusion:
Your company wants to be successful and take good care of its customers. It has more chance of doing both things when it uses an impact recorder on the parcels it’s shipping, which can be easily damaged in transit.
Some shipped items are much more fragile than others, and even a box that looks like it’s in perfect condition can contain an item that’s been harmed through aggressive handling. Because of that, sensing the impact helps catch the problem early on so it can be corrected.
Keep following our page for more such content on shipping and logistics.
Read Also:
Comments Are Closed For This Article