Different Uses Of Sandblasting Cabinets
3 Mins Read
Published on: 01 October 2022
Last Updated on: 08 November 2024
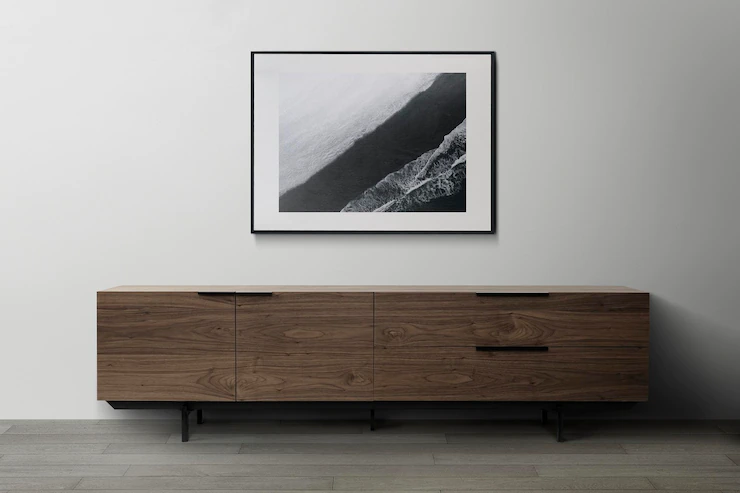
toc impalement
Abrasive blasting cabinets are used for industrial applications on materials and objects. Sandblast cabinets can alter the exterior of components or objects in several ways based on the type of media and blasting circumstances.
Paints can be carefully removed using a softer medium and reduced force. Exceptionally harsh abrasives can be forcefully used to change the pattern or cut objects when applied at elevated pressures.
This adaptable abrasive blasting chamber is ideal for washing, cleaning, and polishing metal components and eliminating rusting, damage, and paint from many surfaces.
Sandblasting Cabinets Usages:
A sand blasting cabinet has many other usages and purposes; the following are a few.
- Cleaning, Enhancing, And Finishing Of Objects
Surface cleansing and scrubbing or eliminating rust, oxide layer, valuable minerals, corrosion grease, grime, coatings, sealants, incomplete combustion, and varnish are made much easier using abrasive blasting.
The most common usage of a sandblast cabinet is for pressure washing or manual cleansing. Paints and coatings can be delicately removed with abrasive blasters without removing the underlying substance.
The abrasive blasting process helps in removing dirt that contaminates surfaces. The dust is taken care of by using dust collectors, separators, and industrial vacuum cleaners.
- Smoothening, Finishing, And Blending
Sandblasting is used for erasing machining and grinding procedure traces or guidelines. Surface treatments can be blended and refined particularly well using spherical materials like steel shot.
The surface becomes clearer and more matte due to the circular corners’ hammering down of better levels. Strong, diagonal abrasive blasting creates a greyer, satin surface with good adhesion properties. The fatigue strength of metals can be increased by 20% to 200% by improving the surface polish. The surface is next refined by being peppered with tiny spheres or microfibers. It is also used to make the surface smooth.
- Removes Rust And Corrosion
The most typical application of sandblasting is to eliminate rust and corrosion. Iron and steel are the most typical ferrous materials where this occurs. A sand blasting cabinet is mainly used to prevent metal rust and avoid corrosion. A pressure blaster with a stronger slicing medium, such as aluminum oxide, is frequently used for such substances.
- Restoring Artwork And Hardware
Abrasive blasting cabinets are used in restoring decorative media by masking or sealing off particular areas. It can blast patterns into glassware, plastics, and metals while keeping the medium confined in the region where it can eliminate profiling the material. This provides a long-lasting, personalized appearance and is a more durable alternative to painting. A blasting cabinet is also used to improve the hardware condition and restore it.
Features to look for in a blasting cabinet
You should have the option to choose between suction or pressure delivery systems, as each has its own advantages. For example, suction-type cabinets are ideal for light-duty cleaning, low-production operations, and occasional maintenance jobs.
Pressure blasts are suitable for aggressive blast cleaning and large-volume applications. However, it requires more maintenance because the components wear out quickly.
Another thing you should look for is an abrasive media recovery system, enabling you to control the particle size. A dust collection and filtration system are also necessary. Some types of dust collectors are baghouse, cartridge, and motorized.
The blasting system is usually of two types: dry and wet, each with distinct advantages.
Dry blasting is compatible with a wide range of materials, allows for faster cleaning, and is suitable for various applications, from surface preparation to high-volume production.
Wet blasting involves low dust production, enables a softer finish on most surfaces, uses fine abrasive media, and can withstand wet contaminants. It is also effective for cleaning partially greasy or oily parts.
Sandblasting removes all types of stains and dirt from surfaces, and surfaces must be prepared for applying paints, adhesives, and sealants. The sandblasting process can be mechanized or carried out by a machine to improve productivity and standard.
Additionals:
Comments Are Closed For This Article