Energy-Saving Devices For Ships: Key Technology For Energy Efficiency In Maritime Transport
5 Mins Read
Published on: 21 July 2025
Last Updated on: 22 July 2025
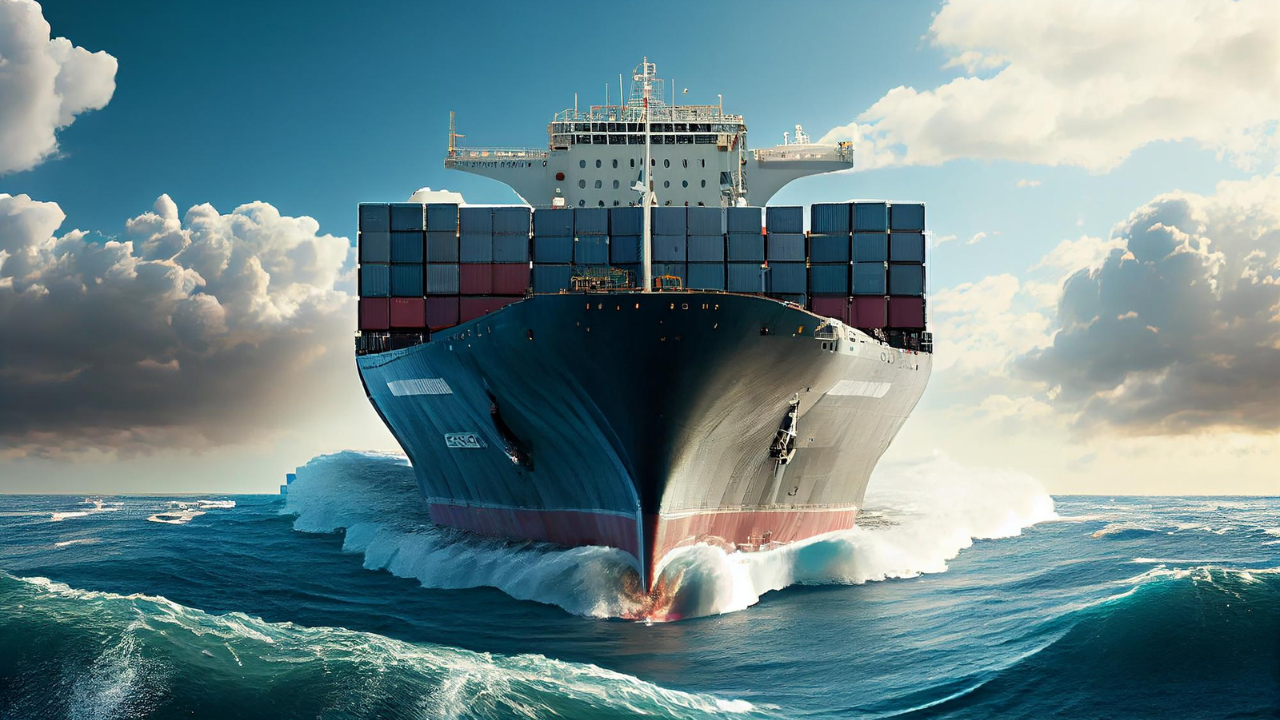
toc impalement
Energy-saving devices for ships (ESDs) have established themselves as effective and cost-efficient solutions for reducing fuel consumption and emissions of pollutants. The reason?
Due to the increasing regulatory pressure and the need to improve the sustainability of maritime transport.
During VICUSdt’s recent webinar, the experts discussed the most relevant energy-saving technology, its advantages, and challenges.
This naval engineering company, specializing in propulsive efficiency, also presented real case studies of its applications.
The Regulatory Challenge And Energy Efficiency
Compliance with current regulations has created an urgent need for shipowners and operators to adapt their fleets. These regulations are:
- The EEXI (Energy Efficiency Existing Ship Index),
- The CII (Carbon Intensity Indicator), and
- The EU Emissions Trading System (ETS)
In this context, ESDs emerge as a viable strategy that enables compliance with the requirements. That too, without resorting to major structural modifications or disproportionate investments.
What Are ESDs And Why Are They Effective?
ESDs are devices installed in the propulsive area that modify the water flow reaching the propeller, optimizing its performance.
This results in improved propulsive efficiency by enhancing various propulsion coefficients of the vessel, such as
- The relative rotative efficiency,
- The vessel’s self-propulsion coefficients.
This thereby reduces the power required to achieve the same thrust.
Through CFD (Computational Fluid Dynamics) simulations, it is possible to design custom solutions that ensure optimal interaction between the hull, propeller, and other devices.
Types Of ESDs And Their Characteristics
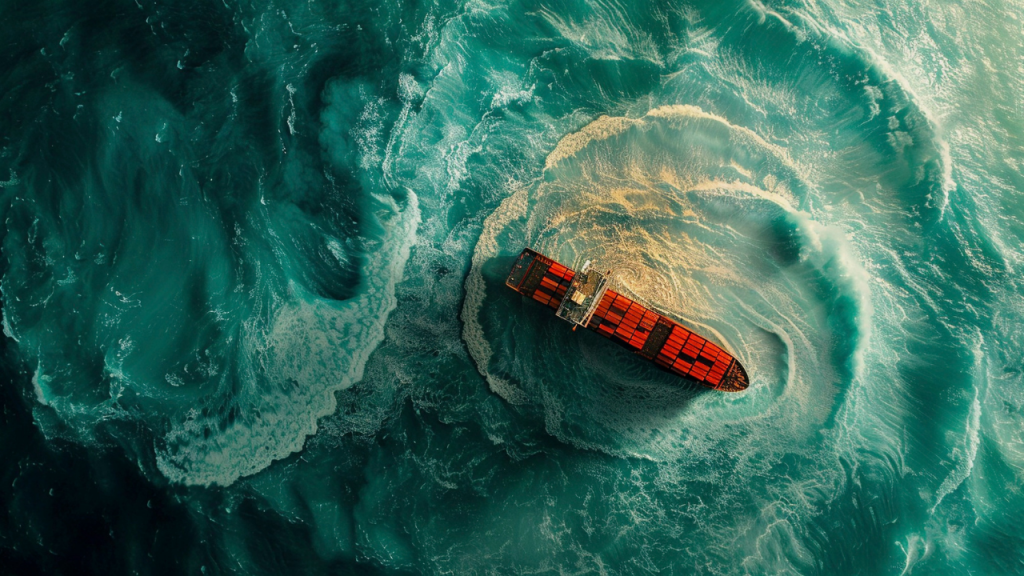
During the seminar, the experts also analysed the main types of devices available on the market, such as:
1. Pre-Swirl Stator (PSS)
Located upstream of the propeller, it acts on the flow rotation, improving relative efficiency.
It is an affordable device, easy to install, and adaptable to different hull types. However, its ability to influence the flow is limited.
Moreover, by modifying the wake, it can alter the propeller’s operating point. Its efficiency improvement ranges between 1% and 6%.
2. Pre-Duct
An older yet still relevant energy-saving technology. It improves the inflow to the propeller, especially in ships with high block coefficients.
Its efficiency gains can range from 1% to 6%, although its transportation, alignment, and installation require careful planning and incur additional costs.
3. PBCF (Propeller Boss Cap Fins)
Fins mounted on the propeller cap that recover part of the vortex generated behind the hub.
It is inexpensive and easy to install, even underwater, but its effectiveness is limited (0.5% to 1.5%).
4. Rudder Bulb And Fins
Devices mounted on the rudder also focused on reducing the vortex generated at the hub.
They generally offer better results than the PBCF (between 0.5% and 3%), although they cannot be installed underwater and may require modifications to the cap in some cases.
5. Propeller Redesign
Although not an ESD per se, redesigning the propeller to adapt to the new conditions created by the ESDs can significantly improve performance.
The efficiency gains range from 1% to 5%, although the cost and complexity of the redesign must be considered.
Combination Of Devices
One common mistake is to assume that savings percentages can be directly added when combining ESDs when it comes to energy-saving technology.
In practice, energy cannot be recovered twice. For example, suppose a pre-duct and a PBCF are installed.
In that case, the latter may have marginal performance if the flow in the hub area has already been optimized, as the remaining vorticity in the hub will be lower.
The ESD located downstream of the hub may even be counterproductive. Proper selection and return on investment (ROI) analysis are essential.
Importance Of Full-Scale Analysis
Model-scale tests (towing tank trials) can overestimate the benefits of certain ESDs due to scale effects, particularly for devices where the boundary layer plays a significant role.
Therefore, it is essential to complement these trials with full-scale CFD studies and compare them with sea trial results.
This methodology ensures more realistic predictions of the devices’ performance in actual operation for energy-saving technology.
In the case of Pre-Duct nozzles, these often show excessively optimistic values in towing tank tests due to the increased thickness of the boundary layer at model scale, which underestimates the resistance generated by the nozzle itself.
These improvements are significantly reduced when the analysis is performed at full scale; therefore, it is essential to evaluate the solution to be implemented directly at ship scale.
Retrofitting And New Designs
ESDs are especially useful in retrofitting projects, as they enable the energy efficiency of existing vessels to be improved without requiring major structural interventions.
However, their integration into new designs from the conceptual engineering stage offers even greater benefits.
Proper planning is crucial for minimizing installation costs and preventing delays during dry docking.
An Integral Process: From Simulation To Implementation
VICUSdt offers a comprehensive approach to implementing ESDs, including technical and economic analysis, custom hydrodynamic design, manufacturing, and support during installation.
This complete value chain ensures that each solution is optimized for the specific conditions of each vessel, backed by objective data rather than assumptions.
Real Cases
During the webinar, several real-world cases were presented of vessels that have undergone a retrofit, where the results obtained in sea trials matched those of the previous CFD simulations.
This reinforces the reliability of the methodology and demonstrates that, with a rigorous technical approach, it is possible to achieve realistic fuel savings—generally between 3% and 7%, depending on the vessel’s configuration and the selected devices.
Conclusion
In a sector pressured by environmental regulations, fuel costs, and the need to remain competitive, ESDs offer an effective and adaptable solution with an attractive return on investment.
However, their implementation requires a thorough technical evaluation, customized design, and a deep understanding of the interaction between hull, propeller, and water flow.
The experience accumulated by VICUSdt shows that there are no universal solutions, but there are effective methodologies to maximize propulsive performance in each case.
Energy efficiency is not an option—it is a necessity. And ESDs are one of the key tools to achieve it.
Read Also: