7 Ways A Warehouse Management System Can Resolve Inventory Issues
4 Mins Read
Published on: 19 March 2022
Last Updated on: 03 July 2023
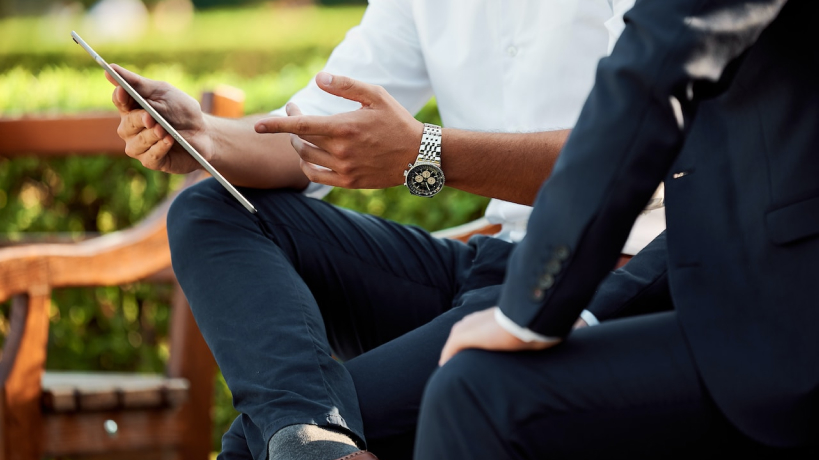
toc impalement
Inventory systems are at the heart of successful warehouse operations. With an effective inventory system, warehouses can monitor raw materials, measure finished goods, and maximize human resources.
However, things can go wrong with inventory systems, calling for resolutions. The following are ways a warehouse management system can resolve common inventory issues.
1. Centralized Tracking
Warehouses that utilize manual inventory tracking systems can, over time, begin to experience redundancy and consistent errors. A computerized system can provide a centralized database that backs up your inventory and gives timely updates.
Human factors primarily cause manual inventory issues. When left unaddressed, the redundancy of manual inventory systems can cause warehouses to lag in their operations and delivery.
Resolving this issue requires a warehouse management system to upgrade to an automated inventory system. Such a system has features for pre-ordering and procurement, thereby improving the accuracy and efficiency of record keeping.
2. Efficient Order Management
Inefficient order management is another common inventory management issue. A discrepancy in product inventory and shortages may occur if orders are not properly handled. Out-of-stock items can also delay production and create an unpleasant customer experience. To tackle this issue, inventory management software can be deployed to automate reorders.
The software will set preorder points based on the stock levels and the availability of goods. That’ll help avoid overselling and enable customers to receive their orders on time.
3. Proper Truck Loading
When a pallet is loaded on the wrong track, it causes several problems. It could lead to an incomplete order. Sometimes, the customer may no longer receive the order. One of the ways to resolve this issue is by ensuring the load checker ascertains the goods being loaded into a truck to be the right ones.
The dispatcher should compare product labels and tags to verify the accuracy of the shipment content. Products that have been wrongly loaded should be removed and kept on the appropriate pallet.
4. Install Protective Elements
Damage is a common issue in warehouses. Damages can lead to goods loss, shipment delay, and loss of sales revenue. Installing protective elements in the warehouse helps to prevent inventory damage.
While it may be challenging to avoid damage within the warehouse altogether, warehouse managers can reduce it. Some ways to minimize damage include installing protective gear such as anti-slip tape, guard rails, and lockout systems.
Another strategy is to make sure the pathways around the warehouse are well-lit and broad enough to allow easy and convenient movement. Early signs of damage should also be detected and promptly addressed.
5. Inventory Forecasting
Inventory forecasting is a way of predicting inventory levels for a future period. This method solves the issue of product unavailability even when the demand has been met.
When a warehouse is unable to predict the correct par stock level, it may be unable to cater to customer demands when they arise. This leads to stockouts. And stockouts a mean loss of revenue.
Inventory forecasting can help you avoid this by accurately predicting future customer demands. With the information from this forecast, you’ll know when to restock and how many units to make available.
6. Workforce Expansion
When warehouse operations expand beyond the capacity of the existing workforce, there’ll be inventory issues. The more rushed and overworked employees are, the more they will be prone to making errors and performing substandard work. To meet operational demands and have your employees perform optimally, you’ll need to expand your workforce.
Begin by looking at the areas of increasing work demands. Also, look at aspects where there are no skilled workers to handle the task. These observations should guide your hiring. Seek out workers who can adequately fit into the available roles and have the right skills to perform allotted duties.
7. Regular Auditing
Auditing is a way warehouses take stock of the goods they have. With regular auditing, you can make accurate predictions of what stocks you have in your warehouse. By doing so, you’ll know which products to restock and which ones to dispatch.
You can audit in various ways. One way is by taking a physical count of all your inventory at once. This can be done yearly or every six months.
Another method is spot-checking. You can spot-check by choosing a product and comparing it with what you see recorded on the software to know if it matches. Through auditing, you can have up-to-date and adequate knowledge of your inventory.
Conclusion
Inventory is a critical aspect of the warehouse management system. However, without properly managing some common inventory issues, you’ll likely lose money and time. In addition, you’ll continue making errors, and getting frequent complaints from customers.
If you’re looking for reliable and efficient order fulfilment services, consider James & James fulfilment services. With their expertise, you can significantly boost your sales, exceed customer expectations, and streamline your operational processes. James & James excels in receiving stock from suppliers, thoroughly checking it for quality, and storing it in their state-of-the-art international fulfilment centres. Their meticulous attention to detail ensures accurate fulfilment and tight stock control, giving you peace of mind.
To avoid this, you should adopt appropriate strategies, such as those recommended in this article, to resolve inventory issues.
Read Also:
Comments Are Closed For This Article