A Small Business Guide to Equipment Tracking
5 Mins Read
Published on: 06 September 2022
Last Updated on: 14 October 2024
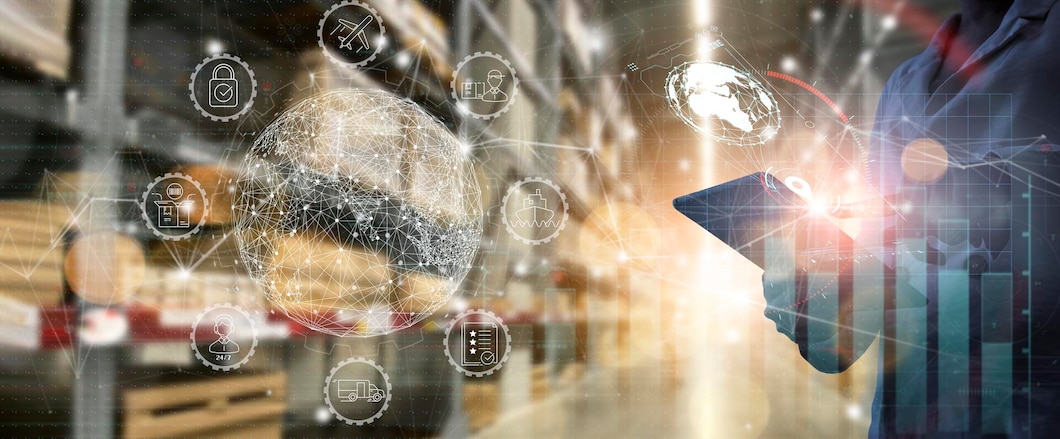
toc impalement
Every organization uses equipment that allows it to speed up its operational activities. These assets usually include computers, printers, company vehicles, internet connectivity, security systems, and office furniture.
When companies regularly audit these assets, they likely identify issues and provide immediate maintenance to ensure efficient performance.
On the other hand, those businesses that don’t track their equipment might lose it. Subsequently, pays for expensive repair costs and reduces productivity due to downtime.
Since equipment tracking is vital in small businesses, startup entrepreneurs must consider following this guide.
Ways to Improve Equipment Tracking:
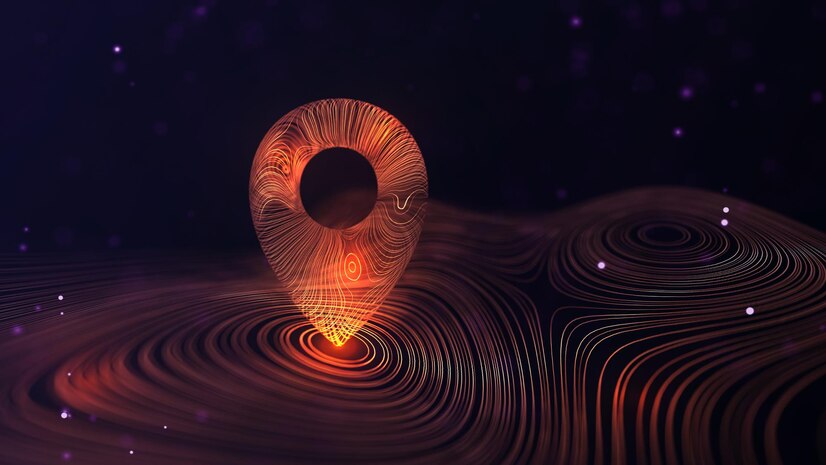
Equipment tracking can only be effective if small businesses have tactics. Therefore, they must consider adopting these five strategies in this process.
1. Make a List of All Office Equipment:
This method is the first step in equipment tracking because entrepreneurs can assess their existing assets.
When making this list, they must record all their equipment and collect accurate details relevant to the users.
These may include purchase date, serial number, asset value, storage address, warranty information, lifecycle end period, and model variant.
2. Develop Equipment Inventory Protocols:
Small business owners must follow this next strategy after listing the total inventory of their office equipment. Thus, they must set a strict policy by specifying every crucial duty and identifying the correct equipment management practices.
For instance, each new asset in their warehouse must be accurately registered into their system.
3. Monitor Loss and Damage:
Start-up entrepreneurs must also consider creating a specific process that indicates what their staff should do after reporting stolen, lost, or damaged equipment. Therefore, they have to generate reporting forms and share them with employees depending on the type of incident.
4. Schedule Maintenance:
Business owners must create a list of maintenance schedules after monitoring equipment loss or damage. This strategy ensures they have all the exact dates for maintaining their technologies to help extend their life cycles.
To improve the efficiency of this tactic, they should automate this activity, allowing them to set system notifications when an asset is close to its expiration period.
5. Use Equipment Identification Products:
Another effective way to improve equipment tracking is by attaching identification products to each piece of machinery.
This method allows entrepreneurs to use a unique code like a quick response (QR) or a reference photo to determine each technological asset.
With that, they must consider purchasing products like nameplates, overlays, signages, and tags from a Metalphoto manufacturer in Cincinnati or near your place.
Benefits of Equipment Tracking:
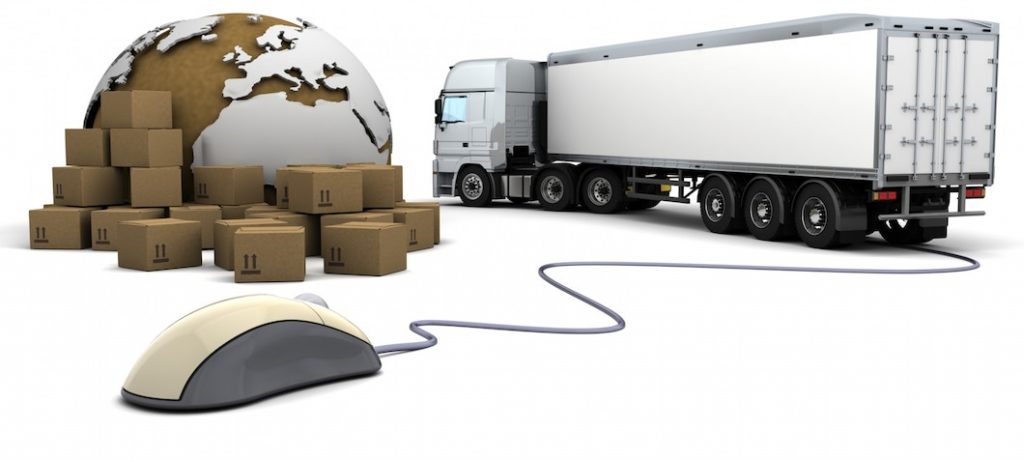
Enabling equipment tracking using modern tools can offer a wide range of advantages for small companies, which include:
1. Reducing Unnecessary Expenses:
When business owners have an effective equipment tracking system, they ensure their staff always have the right tools when necessary.
However, if they don’t regularly monitor their assets, they will likely experience system downtime and lose digital files, forcing them to pay unnecessary costs.
2. Improving Customer Service:
Most consumers only expect the highest possible return on investment (ROI) once they purchase products and services from brands. If the staff can easily use equipment to validate their available resources for specific items, they can be responsive to consumers.
After providing excellent services to them, these companies can generate user-generated content (UGC) from satisfied customers, helping them reach more qualified leads.
3. Enhancing Equipment Performance:
Preventative equipment maintenance can prolong its lifespan, which can help startup business owners avoid costly repairs. When small businesses know when to call assistance to check their support, they will receive their highest possible performance and efficiency.
Instead of replacing their equipment with more advanced and costly ones, they can utilize their existing assets while boosting the efficiency of their companies.
Challenges in Manual Equipment Tracking:
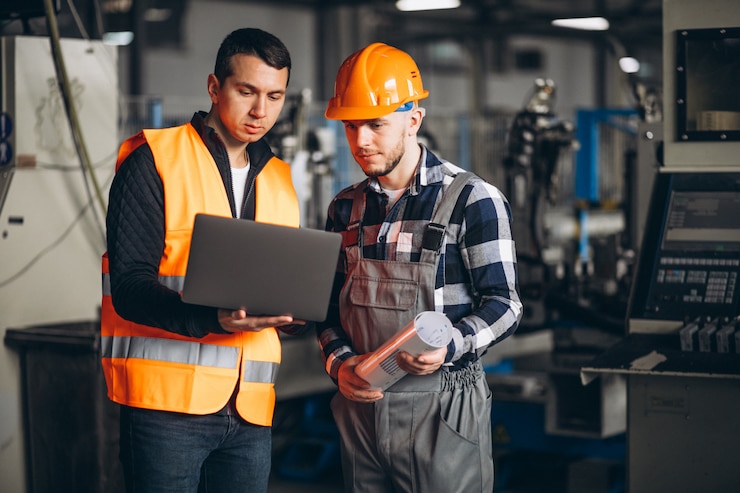
Since equipment tracking is crucial in small businesses, here are five common challenges in this process and ways to prevent them:
1. Outdated Systems:
Most traditional companies that avoid modernization within the workplace need help with obsolete systems. This challenge can make it hard for entrepreneurs to justify manual counting and paper-reliant techniques as they create an inventory of their technological assets.
Instead of continuously struggling with slow and inefficient software, they may save repair costs by replacing their old system with advanced equipment.
2. Theft Occurrence:
Businesses that don’t regularly track their technologies will likely experience frequent theft incidences. Anyone can enter their commercial space and steal easy-to-carry equipment when they don’t have advanced security personnel.
To resolve this challenge, they must invest in technology immobilizers and modern video surveillance, alarm, and motion detection systems.
Also, they must add a global positioning system (GPS) on every asset that allows employees to use a mobile device to scan a barcode label on a tagged tool so they can read its location details.
3. Failure to Return:
If startup owners have purchased defective equipment, the manufacturers have a return and reimbursement policy. This approach means these suppliers will authorize the request and handle the reimbursement or replacement processing.
Therefore, they must invest in modern equipment tracking systems so these companies won’t miss deadlines these distributors have set for valid returns.
4. Human Error:
Employees unintentionally commit workplace mistakes due to lack of sleep and low concentration. Small businesses still follow traditional equipment tracking systems, like manual input in a spreadsheet, which might waste valuable resources.
Thus, they need to consider using inventory management solutions to scan barcode technology to monitor assets as the staff moves them around the warehouse.
5. Maintenance Scheduling:
This issue is one of the biggest obstacles in traditional equipment tracking because businesses don’t know when to schedule preventative maintenance on each asset.
In turn, they have slower production, poor machinery disposal, staff overtime due to systems downtime, and rescheduling of the projects. To prevent this issue, startups must undergo regular inspections, develop strategies, and enable quick responses to alleviate defects.
Key Takeaways:
Startup business owners must ensure that all machinery performs well for smoother operational and production processes.
Therefore, they must consider tracking their technological equipment to avoid costly repairs and reduce theft. Once they do so, they reduce unnecessary expenses, improve customer service, and enhance equipment performance.
Read Also:
Comments Are Closed For This Article